Our Solutions
A Closed Recycling Loop
MSW Recyclers has created the world’s first market-ready process to deliver a closed recycling loop for converting end-of-life tires (ELTs) into recovered Carbon Black (rCB) on a commercial scale. Every tonne of rCB saves 2.5 tonnes of CO2 compared to traditional Carbon Black production.
The result of our process is a mutually beneficial conversation between two challenges. On the one hand, our solution for ELTs addresses the question of the disposal of ELTs in an environmentally responsible manner. The use of rCB in tires allows the tire industry to “close the loop” on ELTs, something that has never before been possible and will yield invaluable possibilities for new generations of green tires. Second, the substitution of rCB results in a decreased environmental footprint for Carbon Black production.
The MSW Recyling process is an example of the circular economy at work, taking one key input (ELTs) and producing four commercial outputs:
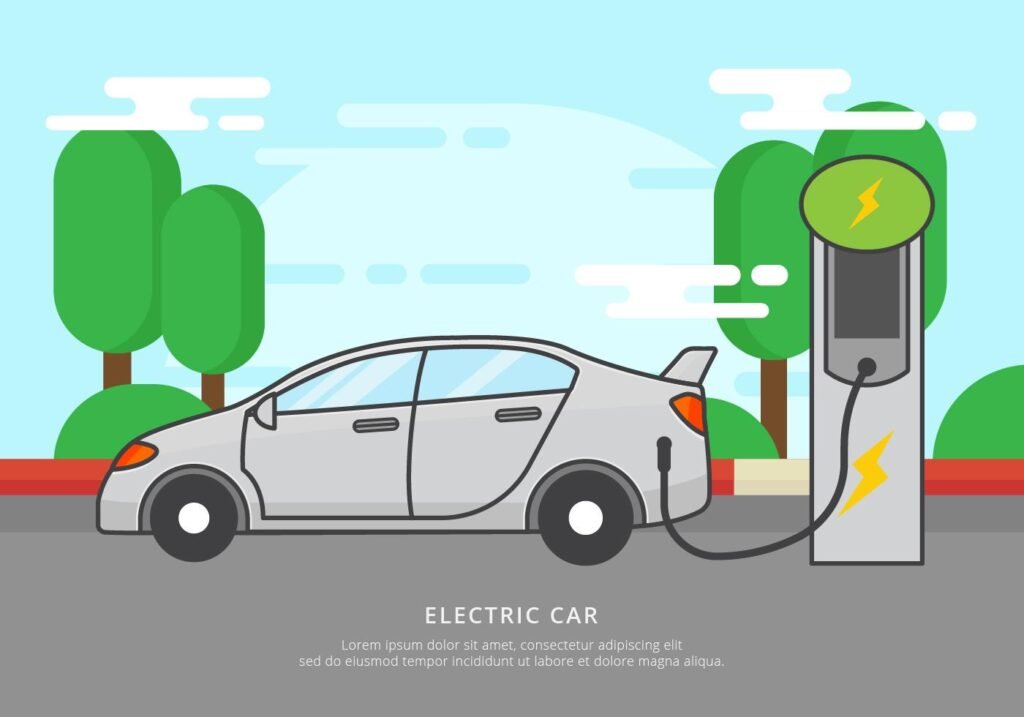
01. Recovered Carbon Black
MSW’s core product for sale and use in the tire, mechanical rubber goods and plastic industries.
02. Pyrolysis Oil
This can be used as fuel oil or feedstock (for example, in synthetic gas (syngas) production) or can be further refined and blended with heating oil.
03. Steel
For every ton of tires processed, MSWreclaims .16 tons of steel for potential commercial use, reducing waste and the environmental harm caused by manufacturing new steel.
04. Gas
The gas output has a calorific value comparable to natural gas and can be reused in the MSW process to produce energy or heat.
Reduced CO2 Emissions
MSW’s closed-loop solution addresses the global problem of mounting harmful emissions. Compared to traditional carbon black production, every ton of recovered carbon black we produce saves 2.5 tons of C02. Every MSW 20 oven plant saves approximately 32,000 tons of C02 from being released into the environment annually.
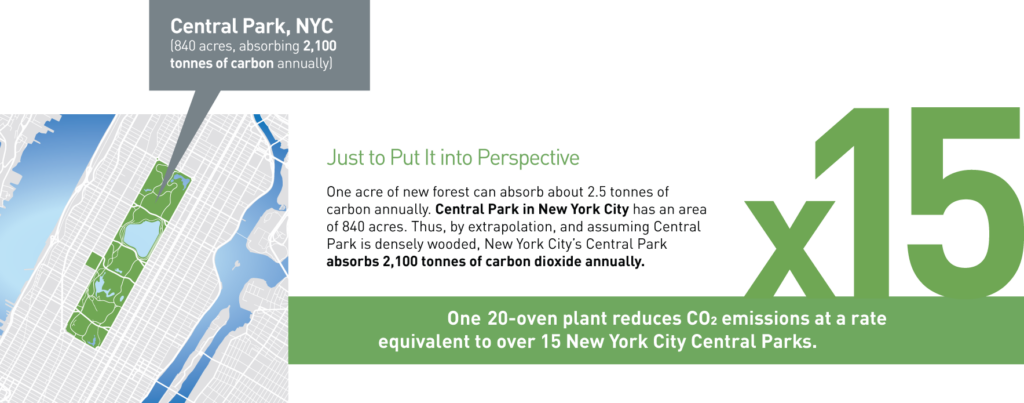
Recovered Carbon Black Benefits
Recovered Carbon Black (or rCB) is a material derived from scrap tires by pyrolysis. While rCB can be utilized in all the same ways as virgin Carbon Black, its production process is vastly superior to the latter’s in that it is sustainable, cost-efficient, and can meet growing consumer demand without compromising the environment.
Based on customer feedback and application testing, MSW estimates that recovered Carbon Black can substitute for virgin Carbon Black at rates from 10% up to 100% depending on the application.

10-30% rCB
- Passenger car/light truck tire tread
- Heavy duty conveyor belts (mining, etc.)
- High pressure hoses
- Transmission belts
30-50% rCB
- Passenger car/light truck tire sidewall
- Passenger car/light truck tire undertread
- Passenger car/ light truck body and belt plies
- lndustrial/agricultural tire tread and carcass
- Light/moderate duty conveyor belts
- Rubber sheeting/geomembranes
- Wirecable jacketing
- Gaskets & seals
- Rubber roofing
50-100% rCB
- Passenger car/light truck tire innerliner
- Passenger car/light truck tire bead/apex
- Plastic masterbatch (for general plastic compounds)
- Polyolefin films (trash bags, agricultural film)
- Plastic pipe
- Newspaper inks
In addition to these various applications, rcB offers a multitude of competitive advantages over virgin Carbon Black, presenting not only a superior footprint but also a higher-quality and more cost-efficient alternative.